金属加工を行う設備は、適切な状態の潤滑油を用いることで摩擦や摩耗を低減し、部品や加工対象の発熱を抑制することが可能です。しかし、設備の稼働を続ける過程で潤滑油が劣化してしまうと、潤滑油本来の機能を果たせずに、設備寿命の劣化などに繋がります。
加工設備を長期間安定して使用するには、定期的な設備の点検や潤滑油の交換が必要です。効率的に潤滑油の状態を把握し、適切なタイミングで交換するために、近年は予知保全を用いた潤滑油の状態分析技術が開発されています。
本記事では、金属加工設備における潤滑油の役割と劣化における影響、予知保全による潤滑油の分析について紹介します。
この記事でわかることを簡単にまとめると…
- 金属加工設備における潤滑油は、摩擦・摩耗・発熱の抑制、不純物除去などを担う
- 金属加工設備の潤滑油が劣化することで設備劣化や品質低下を引き起こす
- 設備を維持する保全には、主に事後保全、予防保全、予知保全がある
- 予知保全を導入することで、適切なタイミング・箇所のメンテナンスが可能
- 潤滑油の保全タイミングを判定する際には、色や誘電率の変化が活用できる
「ミニマリストの片付け」を運用するトレファクテクノロジーズが、広範なBtoBライターネットワークを活かし、専門性の高い各種コピーライティング、メディアを活用した記事広告施策など、ご要望に最適なライティング施策やSEOコンサルティングをご提供いたします。
金属加工設備における潤滑油の役割
金属加工において、加工設備が稼働する際には部品や加工物が触れ合うことで摩擦が発生し、それによる摩耗や発熱が生じます。潤滑油は、触れ合う部品や加工物の間に入り込み、摩擦や摩耗を低減する役割を担っています。
金属加工設備に潤滑油を用いる代表的な役割と、その効果は以下の表の通りです。
役割 | 概要 | 効果 |
摩擦抑制 | 部品間の摩耗を抑制し、設備全体の滑らかな動作を維持する | 設備の稼働効率が向上し、設備稼働に必要な燃料の消費量を低減 |
摩耗抑制 | 部品間の衝撃を吸収・緩和し、部品同士の摩耗を抑制する | 設備を構成する部品の摩耗を低減することで、設備を長寿命化 |
発熱抑制 | 設備運転中に生じる熱を吸収・分散する | 設備の発熱を防ぐことで、熱変形や耐久力の低下、破損を防止 |
不純物除去 | 設備内部に蓄積される不純物を除去する | 不純物による設備の動作抵抗を抑制し、本来の性能を維持 |
腐食・錆防止 | 設備部品表面に保護膜を形成し、水分や空気などによる腐食を抑制 | 腐食や錆による部品の交換、修理頻度を低減。メンテナンスコスト抑制 |
このように、潤滑油はさまざまな役割を担っています。
金属加工設備の潤滑油が劣化することによる影響
金属加工設備の潤滑油を適切に交換せずに、劣化した状態で使用し続けることで以下のような影響が生じます。
金属加工設備の劣化
摩擦や摩耗の抑制という役割を担っている潤滑油が劣化すると、設備部品の摩擦や摩耗が増加してしまい金属加工設備の劣化が進行しやすくなります。また、潤滑油の冷却作用がうまく働かないことで設備が高温状態で稼働することになり、熱疲労が生じることも設備が劣化する要因の一つです。
設備や部品の種類によって異なりますが、状況次第では長時間設備の稼働を止めないと摩耗した部品の交換ができません。あらかじめ計画していた生産計画からの遅れが生じることで、顧客にも影響を与えることになりますし、売り上げの低下にも繋がります。
製品品質の低下
劣化した潤滑油を使用し続けることで、対象の金属加工設備で製造する製品の品質劣化が生じるリスクがあります。
加工設備の部品が摩耗した状態で製造を続けると、製品の寸法ずれが生じてしまったり、製品強度が不十分になったりする可能性があります。また、潤滑油が十分に不純物を除去できないことで、製造した製品に不純物が混入してしまうリスクもあるでしょう。
製品品質の低下は、製品の機能を低下させてしまうだけでなく、内容次第では顧客からの信頼を大きく失う事態になりかねません。高い製品品質を維持するためにも、潤滑油を適切な状態に保つ必要があります。
金属加工設備の状態を維持する保全
金属加工の劣化による影響を防ぐためには、適切に設備の保全を行うことが重要です。保全とは、設備の状態を把握し、安定して安全に稼働できる状態を維持することを意味します。また、設備に発生した故障や異常に対して、適切な処置を行うことも保全の一部です。
従来、保全活動は主に「事後保全」と「予防保全」の2種類に分類されていました。
事後保全は、機械加工の設備が故障したら故障した部分を修理、メンテナンスするというものです。故障してから初めて保全活動を行うため、修理規模が大きくなる傾向があり、その期間は設備を止める必要があります。
事後保全の場合に生じる故障や修理期間の影響が大きいことから、故障や異常が発生する前に定期的に部品を交換する予防保全が行われるようになりました。しかし、予防保全では部品を寿命の近くまで十分に使いきれない場合があります。
また、部品の交換タイミングは経験や勘に基づいて行われることが多いため、根拠が科学的ではありません。メンテナンスにかける部品やコストのムダが、多くなってしまうリスクがあります。
予知保全とは
事後保全や予防保全のデメリットを解消するために、予知保全に取り組む企業が増えています。予知保全とは、対象となる機械加工設備を通常通り使用しながら設備の故障や異常の兆候を検出し、その結果に基づいて保全業務を行うことです。
設備の状態を把握するためには、トルクや圧力、振動などの機械的信号、電流や電圧、磁束密度などの電気磁気的信号などを用います。また、色や水分などの化学的信号を予知保全の情報として用いる場合もあるでしょう。
予知保全では、その目的に応じてこれらの情報から故障や異常の兆候をつかみます。どの情報を用いるのか、どの程度の水準に到達したら保全業務を行うのか。これらを適切に設定するためには、さまざまなデータの分析や知見・経験が必要不可欠です。
また、予知保全には状態を検出するためのセンサや分析を行う監視システムを導入する必要があります。導入には大きなコストが必要になる場合があるため、費用対効果を十分に検討して導入判断をする必要があります。
「ミニマリストの片付け」を運用するトレファクテクノロジーズが、広範なBtoBライターネットワークを活かし、専門性の高い各種コピーライティング、メディアを活用した記事広告施策など、ご要望に最適なライティング施策やSEOコンサルティングをご提供いたします。
予知保全による潤滑油劣化の確認方法
機械加工設備で用いられる潤滑油の劣化を予知保全によって検出する際には、色による判断と誘電率による判断が考えられます。
潤滑油の色の変化
潤滑油は、使用し続けることで異物の混入や潤滑油自体が酸化するため、徐々に色が変化します。潤滑油の劣化を色で診断する方法として、ASTM番号を基準にすることが可能です。
通常、潤滑油の色の変化は目視で確認を行います。しかし、近年は高性能で小型のカメラが開発されており、未使用の潤滑油の色に対してASTM番号でどの程度の色の変化が生じているかを自動検出することが可能です。
潤滑油の色に影響を与える透明度は温度によっても変化するため、色と温度の情報をうまく組み合わせることで、人間が目視で確認するよりも高い精度で劣化状態を検出できる可能性があります。
潤滑油の誘電率の低下
潤滑油の劣化を引き起こす原因として、酸化物や鉄粉、水分などの不純物の混入が考えられます。これらの不純物は誘電率が高いことから、潤滑油の誘電率を測定することで潤滑油の劣化を判定することが可能です。
誘電率は、測定に必要なセンサを取り付けていれば、色の変化と同様にリアルタイムで検出することが可能です。潤滑油の劣化を速やかに検出できれば、対策も速やかに行うことができるため、潤滑油の劣化による影響を最低限に抑えられます。
※こちらの記事の内容は原稿作成時のものです。
最新の情報と一部異なる場合がありますのでご了承ください。
この記事を書いた人
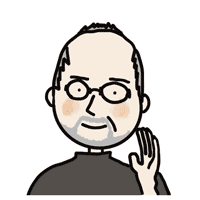
スマホはジーンズのポケットにいつでもイン。「ミニマリストの片付け」編集部スタッフが、さまざまな記事をお届けします。